
High-Precision Laser Welding Transforms Microfluidic Chip Design
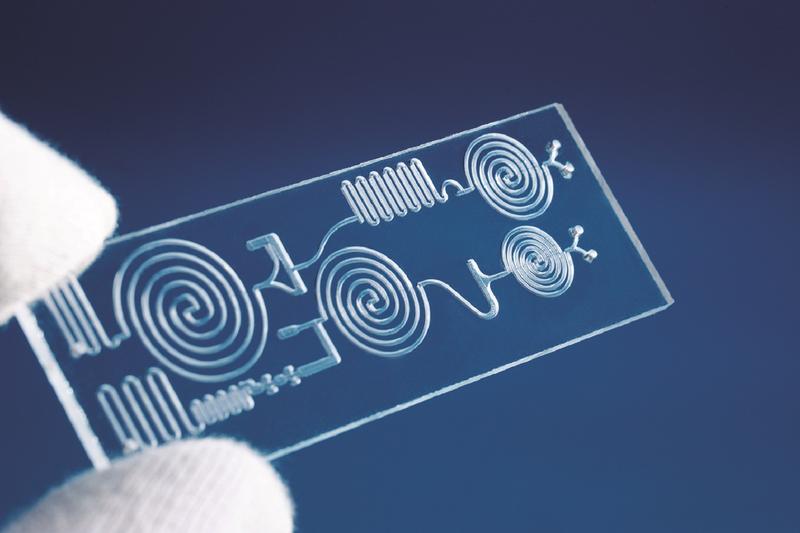
In the SeQuLas research project, the partners developed an electronically monitored process for gentle, high-precision laser transmission welding of small plastic components for medical technology.
© Fraunhofer ILT, Aachen, Germany
In the life science sector, microfluidic chips have proven their worth since they can transport, mix and filter even the smallest amounts of liquid efficiently. They still pose a major challenge, however: the media-tight encapsulation of the microchannels integrated in the chips.
Conventional joining technology reaches its limits in the micrometer range. In its place, absorber-free laser transmission welding (LDS) – with beam sources in the near-infrared (NIR) range – allows high precision and flexibility, making it the ideal solution here.
Transparent components thanks to the absence of absorbers
And that is why Fraunhofer ILT launched the SeQuLas project in 2017, together with Amtron GmbH from Aachen, Ortmann Digitaltechnik GmbH from Attendorn and Bartels Mikrotechnik GmbH from Dortmund.
The project was funded under the »Produktion.NRW« program of the LeitmarktAgentur NRW, and the acronym SeQuLas stands for »segmental quasi-simultaneous laser irradiation«. Here, a thulium fiber laser with an emission wavelength of 1940 nm was used as the beam source; plastics have a natural absorption in this wavelength range.
Since additional absorber material such as soot is not necessary, the transparency of the chip is not affected during laser processing.
However, this form of absorber-free laser transmission welding has a problem: Volume absorption creates a heat-affected zone (HAZ) that extends vertically over the entire cross-section of the component. The thermal expansion during the melting process promotes the formation of blowholes and cracks, which cause leaks in the seam structure. In addition, there is a risk that the material will warp, especially in flat components.
Quasi-simultaneous irradiation for gentle heating of materials
Quasi-simultaneous irradiation can be used to reduce the heat-affected zone from expanding vertically. In this process, a laser beam is guided several times along the weld contour at high speed with the aid of a scanner system: Thanks to this, the entire seam contour is heated simultaneously, which otherwise only melts sequentially in contour welding.
In tests with polycarbonate components, Fraunhofer ILT has demonstrated that during the welding process the heat is dissipated at the outer surfaces while heat accumulates inside the material. The increasing number of passes and the high scanning speed even reduce the vertical expansion of the heat-affected zone by up to 30 percent compared to contour welding.
Early detection of thermal damage
In a second step, the project partners developed a process control for the laser welding process. A pyrometer integrated in the beam path measures the temperature in the component during the welding process. By coupling the measurement signal with the position of the scanner mirrors, they have made it possible to record the heat distribution in the component in a spatially resolved manner.
In this way, thermal damage can be recorded and precisely localized during the welding process. The newly developed welding process can, therefore, react quickly to temperature deviations and control the laser power accordingly. In this way, homogeneous seam properties along the seam contour can be ensured.
The project »SeQuLas – Laser Welding of Absorber-Free Thermoplastics by Segmental Quasi-Simultaneous Irradiation« was completed in February 2020 and ran for three years. It was funded by the European Regional Development Fund (ERDF) and the state of North Rhine-Westphalia.
M.Sc. M.Sc. Phong Nguyen
Micro Joining Group
Telephone +49 241 8906-222
phong.nguyen@ilt.fraunhofer.de
Dr.-Ing. Alexander Olowinsky
Micro Joining Group
Telephone +49 241 8906-491
alexander.olowinsky@ilt.fraunhofer.de