
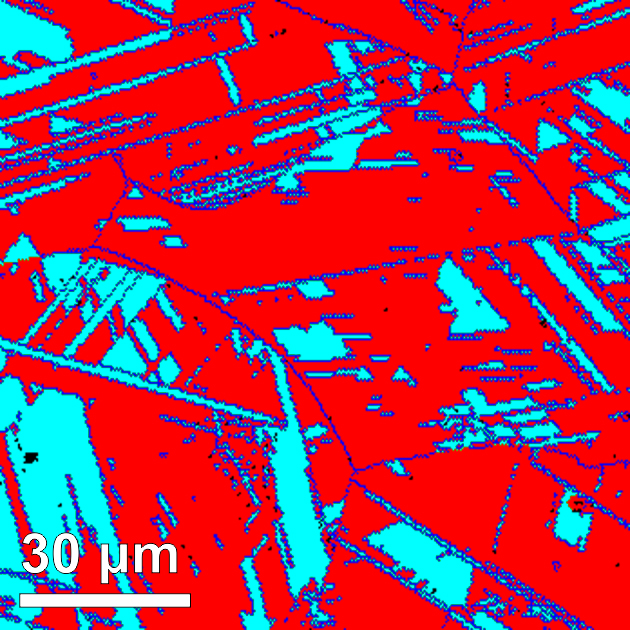
A strong alloy made of iron, manganese, cobalt and chrome becomes ductile because it can have two coexisting crystal structures, and one structure can transform into the other.
Nature 2016 / Max-Planck-Institut für Eisenforschung GmbH
Ideally, steels and steel-related alloys should be capable of both properties: they should not fragment, for example during processing in a mill or as car bodies involved in an accident. In other words, they must be “ductile”, as materials scientists refer to it.
However, they also need to be strong so that they do not warp or break when subjected to weak forces. A team headed by Dierk Raabe, director at the Max-Planck-Institut für Eisenforschung, and Cemal Cem Tasan, formerly head of a research group at this Institute and now professor at the Massachusetts Institute of Technology in the US, has now succeeded in combining both properties in one material. To date, extremely ductile metallic materials were not particularly strong and vice versa.
“We pursued a new strategy in the development of this material, which generally opens up new possibilities for the design of metallic materials,” says Dierk Raabe. The team began at a type of material that has been the subject of extensive testing by materials scientists in recent years, but which was too brittle for many applications up until now: alloys in which metallurgists combine similar quantities of typically five or more different metals.
Atomic disorder enables high-strength alloys
As the atoms of the different elements are distributed along the positions in the crystal lattices of these materials without any identifiable order and the entropy is, to a certain extent, a measure for the disorder, the materials are called high-entropy alloys. Such materials can be particularly strong because the disorder of the numerous different atoms in a structure makes it difficult for dislocations to move.
Dislocations are defects in the crystal lattice that move through a crystal when a material becomes deformed. However, there has been one disadvantage to the high strength of the alloys with atomic disorder till now: when such a material gives way under pressure, it is usually brittle.
Steels that mainly contain iron, usually another main component and small quantities of other elements like carbon, vanadium or chrome, are, on the other hand, often ductile. They are not brittle; however, up until now they have not been strong enough to enable, for example, the construction of car bodies with thinner sheets.
In the crystals of steels, the atoms are more or less regularly arranged. Steels become particularly ductile though if they can switch from one structure to another. This is because this process swallows energy, which can then no longer initiate any damage in the material. In a car body or other steel components, tiny areas then alternate with the two different atom arrangements.
The change in the crystal structure makes the material ductile
It was precisely this coexistence of the different crystal structures that was detrimental to the high-entropy alloys – thus far. “We have now turned this conception on its head, as recent studies have shown that this is not the important factor,” says Zhiming Li, who made this scientific turnaround the topic of his project. Together with his colleagues, Li searched for a material that is, on the one hand, as strong as a high-entropy alloy, but, like particularly ductile steels, has two coexisting crystal structures. The search produced an alloy made from 50 per cent iron, 30 per cent manganese and 10 per cent respectively of cobalt and chrome.
“With this alloy, we have shown that our concept works,” says Raabe. “If we further improve the microstructure and the composition, we can even further enhance the strength and ductility.” This is precisely the area the researchers are now working on. This means that they could, once and for all, solve the metal-processing industry’s dilemma of having to choose between strong or ductile materials.
The metallic materials from the Düsseldorf-based materials forge could be processed just as easily and cost-efficiently as a particularly ductile steel and absorb as much impact energy in an accident when incorporated in the body of a car. At the same time, the material would be strong enough that thin and thus low-cost and resource-conserving metal sheets do not give way when subjected to a weak force.
Author: Peter Hergersberg, Max Planck Society