
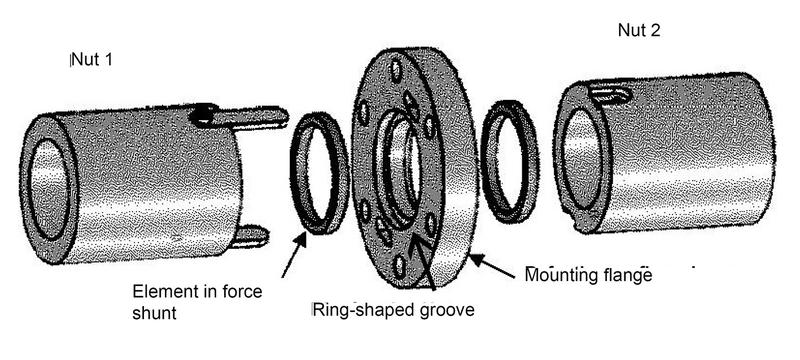
An invention of the University of Stuttgart combines a high rigidity and thus a high precision and long life, with a minimum of preload.
Grafik: TLB GmbH
Ball screws or ball screw drives are gear arrangements with rolling balls inserted between a screw and nut element. They are used to translate rotational motion to linear motion or vice versa. In comparison to conventional screw gears with dominant sliding friction, where approximately 50 to 90 percent of the power is converted into heat, ball screw drives work with less friction, high positioning accuracy and reduced wear. The higher production costs can be justified by the practical advantages and a longer lifetime. More than a third of machine tool failures are due to fatigue fractures of ball screws.
In order to provide the required precision and rigidity of a ball bearing spindle, a contact preload can be applied using so-called double nuts. However, large axial forces can produce an overload situation during which one of the two nut halves is completely unloaded. As a result, excessive sliding movements and a rupture of the lubricating film may lead to an early destruction of the ball bearing spindle.
To avoid this, the preload is usually set sufficient high, which leads to excessive more friction and thus higher wear. This in turn negatively affects the accuracy and lifetime of the spindle. Moreover, a lower preload reduces the mechanical and thermal load on the ball screw drive and increases its expected lifetime.
A constant preload can, for instance, be implemented by inserting a spring element between the two halves of the nut, as done in the case of alternative double nut systems (Fig. 1). However, due to the high elasticity of the spring element, these systems are not suitable for high-accuracy or high-dynamic applications.
At the University of Stuttgart, Dr.-Ing. Siegfried Frey succeeded in developing a solution that combines a high rigidity and thus a high precision and long life, with a minimum of preload.
Between the two nut halves of a symmetrical double nut, additional elements – with an e-module lower than that of the nut materials – are inserted, for example within a ring-shaped groove (Fig. 2). These are located in the force shunt, between the nut and clamping flange and simply remain in static condition – contrary to conventional solutions with spring elements.
However, for high axial loads, the preloaded elements escape the force shunt and create a residual preload in the unloaded nut half, avoiding total unloading. This prevents excessive sliding movements. Due to the arrangement of the spring elements in the force shunt, there is nearly no impact on the rigidity of the overall system. The residual preload can be controlled by the parameters of the elastic element.
This invention allows to preload ball screw drives easily and cost-effectively with a significantly lower load, but without any negative impact on the rigidity and accuracy of the overall system. The solution is suitable for a wide range of ball screw drives, especially for tool machines with high performance requirements. Depending on the application and the type of load, the invention can increase the life of a ball screw significantly, while maintaining the required precision and rigidity.
Patents for the invention were granted in Germany (DE10 2009 0499 36B4) and a European application (EP) was filed. Technologie-Lizenz-Büro (TLB) GmbH supports the University of Stuttgart in patent-related matters and in marketing its innovations. The University of Stuttgart has entrusted Technologie-Lizenz-Büro (TLB) GmbH with the economic implementation of this cutting-edge technology and offers companies the possibility of obtaining licenses or purchasing the patents.
For further information, please contact: Innovation manager Dipl.-Ing. Emmerich Somlo (somlo@tlb.de)
http://www.technologie-lizenz-buero.com/