
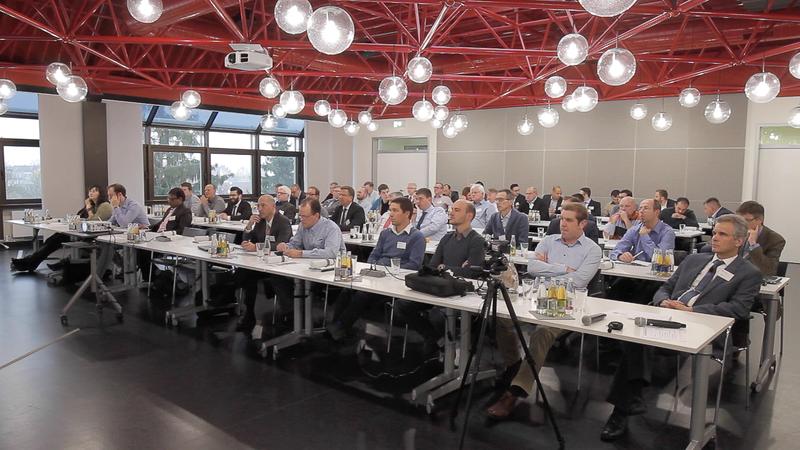
Around 50 specialists from Europe, Asia and the USA met in Fraunhofer LBF for the UC 13 – Users Conference on Biaxial Fatigue Testing for Wheels, Wheel Hubs and Wheel Bearings.
Photo: Fraunhofer LBF
The wheel-related components of the chassis, i.e. wheels, wheel hubs and wheel bearings, are safety-relevant components subject to high levels of stress. Given the complex requirements governing functionality and safe service life, wheel-related components have been a focus of Fraunhofer LBF for many years.
The Darmstadt specialists have been organizing the international users conference for scientists, automobile and commercial vehicle manufacturers and suppliers for 26 years now. The meeting is a forum where scientists and users from Europe, Asia and the USA discuss new developments on the market for testing technologies and trends in testing and production technologies.
Biaxial wheel-testing technology is now known and accepted all over the world and has increasingly become established as an international standard for greater safety in vehicle construction. This is also apparent in the profile of the visitors, which in recent years has become ever more international.
At this year’s conference, current topics relating to testing procedures and techniques for passenger and commercial vehicles took center stage in various sessions. For example, new findings regarding load data for wheels and wheel hubs on triaxial semi-trailers, the testing of plastic wheels and the increasingly popular tires with emergency running characteristics and their effect on wheel stress were presented.
Fraunhofer LBF interspersed this with live demonstrations of the latest “wheel/hub strength” software. The software allows the component’s lifespan to be numerically simulated, which enables optimal development before production of the component gets underway. To round off the conference, the participants were given a tour of the laboratory, where they were given a close look at the institute’s testing equipment.
Fraunhofer LBF is considered a pioneer in multi-axial service life verification for vehicle wheels. Scientists from the institute first put the biaxial wheel/hub testing station (ZWARP), a then cutting-edge facility for testing vehicle wheels under biaxial stress, into operation in 1982. It was patented in 1984 for road vehicles and in 1987 for railway vehicles and was subsequently sold to customers under license.
Fraunhofer LBF has its own website, www.zwarp.de, which holds detailed information on the biaxial wheel/hub testing station (ZWARP). Wheel/road simulators of this type are today used all over the world to shorten development times in the automobile industry and to test safety components such as wheels and wheel hubs.
http://www.zwarp.fraunhofer.de/en/lbf-biaxial-wheel-hub-fatigue-testing.html