
Guides for Medium-Sized Enterprises by University of Stuttgart
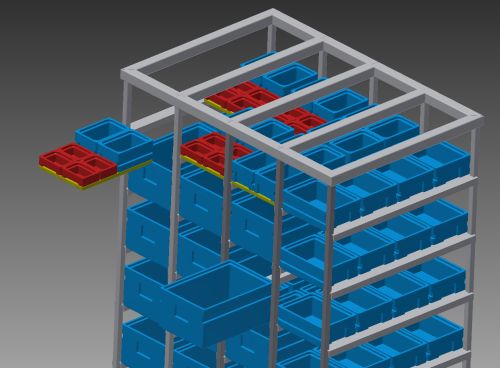
To make production logistics more flexible, current standardised load carriers (below) are to be equipped with communication technology and supplemented with small trays.
Photo: University Stuttgart/IFT
For over 100 years assembly in the automobile industry has gone in cycle sequences in which it is precisely determined when, where and how a certain work step is to take place.
For production logistics this means that the materials must also be delivered to the conveyor belt according to this cycle. This system has led to goods being able to be produced efficiently, quickly and above all cost effectively.
However, this is too rigid for the requirements of today’s adaptable production with increasingly numerous product variations in increasingly smaller quantities. In the framework of the research campus ARENA2036 the Institute of Mechanical Logistics and Logistics (IFT) at the University of Stuttgart is working on solutions enabling more flexibility and changeability and is drawing up a guideline with the support of the State of Baden-Württemberg for smaller and medium-sized companies. This could lead to electric cars in particular becoming cheaper.
Today in the automobile industry vehicles go through the final assembly from a clocked belt or similar conveyor technology. Specific parts are made available and assembled at each assembly place until the complete vehicle ultimately leaves the production hall.
This system has its strengths if the assembly stations are to be supplied with similar or identical materials in larger quantities – in borderline cases with all parts that are needed for the vehicles to be assembled in the next shift. In view of a greatly increased number of variations in the automobile industry (for example of the 1.1 million sold Mercedes A-Class cars from the latest model range only two were identical), however, clocked production reaches its limits: here only the parts are to be made available that are needed for the assembly of a specific vehicle, which leads to an explosive increase in logistics costs.
The development of electro mobility aggravates this issue since the complexity in production increases further with the parallel production of hybrid and electric vehicles – a reason for electro vehicles being disproportionately expensive. The Stuttgart scientists want to overcome this hurdle through using innovative assembly stations, individual material provision concepts and improvements in the changeability of production. The findings are to be transferred to other areas of the producing industry.
One of the centrepieces of the logistic solutions developed at IFT form intelligent, self-controlling load carriers as well as innovative storage elements. The load carriers common in the automobile industry of the small load carrier type with a size of 600 x 400 x 280 millimetres, of which around 30 million items are in circulation, do not communicate and are lined with disposable inlays to protect the transported goods. Future load carriers in contrast are to be padded with an innovative filling material in which an RFID tag as well as a position finding unit are integrated.
The equipping of the load carriers with communication and position finding systems enable the localisation of the carrier in the room as well as the data exchange and the integration of the carrier in the overall control of the assembly plant. Since the dimensions of the current small load carriers for the single delivery of model components in addition are too large and give away transport capacities, the IFT is devising trays on the basis of the basic small load carrier dimensions in which smaller containers can be used.
Arranged in bars, the trays and small load carriers are to be received in future by innovative warehouse elements and handled automatically. The conveyance is done with the help of driverless transport vehicles (FTF).
In order to keep the model number of these transport appliances low and to guarantee a high level of utilisation of the units in operation, a universal concept is to be developed that is based on the principle of a carrier platform with exchangeable accessory equipment and has various functional interfaces. The special feature of this new automatic warehouse is providing material “just in real time“ (JIR), since the current delivery “just in sequence“ (JIS) cannot react quickly enough to changes.
The scientists from the IFT are preparing their research results into a freely accessible guideline for medium-sized companies that show the implementation of the innovative logistics concepts including their connection to linked load carriers and a bar concept.
The guideline is also to focus on why changes are necessary in production logistics in order to cope with an increasing diversity of models. The Ministry for Finances and Economic Affairs Baden-Württemberg funds the project with around 160,000 Euros.
Further information:
Prof. Karl-Heinz Wehking, University of Stuttgart, Institute for Conveyor Technology and Logistics, Tel. 0711/685-83770, Email: Karl-Heinz.Wehking (at) ift.uni-stuttgart.de