
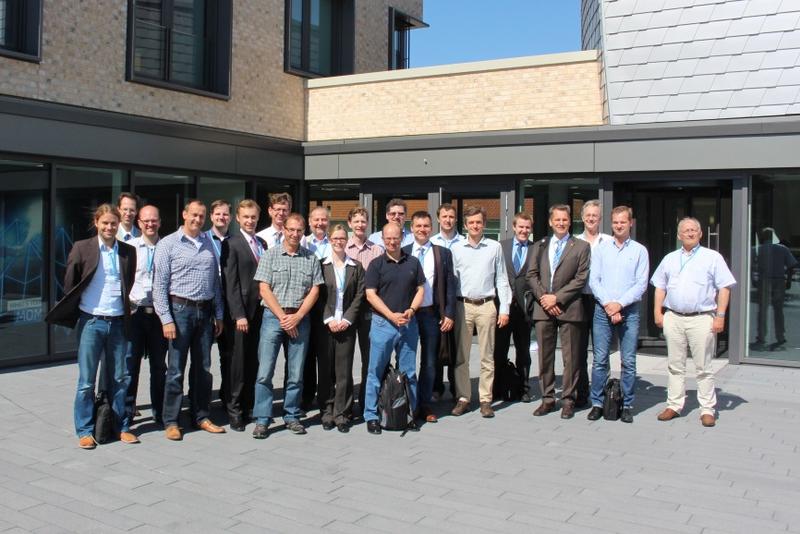
Participants at the Kick-Off-Meeting in July, in front of the Sennheiser Innovation Campus.
Photo: Sennheiser
For a hearing aid or an individualized in-ear-headset, presently a mold of the ear is made, then digitized and finally used to manufacture the otoplastic. The project partners of 3D-PolySPRINT want to fundamentally change this approach.
Digital Mold of the Auditory Canal
Using the non-tactile imaging method of optical coherence tomography (OCT), they want to make a digital image of the auditory canal without having to make a mold. First the ear is optically scanned, and the form is digitized.
For the next step, the group Image-Guided Laser Surgery of the LZH is developing a software which converts the raw image data of the scan to a construction file. Once in the computer, the data can be further processed quickly, and molds do not need to be sent to other sites, and then scanned.
A hard core and a soft covering
Using the digitized data of the individual ear, the partners want to optimize both the function and the wear comfort of the ear mold for the customer, and avoid unpleasant pressure sores. To achieve this, the partners are combining two additive manufacturing processes, spray coating and Laser Transfer Printing (LTP), in order to join two different materials together, and to make a hardness profile within the ear mold.
The Laser Micromachining Group of the LZH is developing the necessary process, and is examining the new materials concerning their suitability, always keeping the criteria of the end users Sennheiser electronic GmbH & Co KG and KIND Hörgeräte GmbH in mind.
Increasing wear comfort and decreasing delivery times
With this innovative process chain of OCT and 3-D printing, not only the manufacturing of the otoplastics is considerably more pleasant for the customers. Also, the headset or the hearing aid would be usable for longer periods of time, it would provide better sound quality, and it would reach the customer at least a day earlier.
About 3D-PolySPRINT
The joint project 3D-PolySPRINT is being coordinated by the Sennheiser electronic GmbH & Co. KG and consists of the companies KIND Hörgeräte GmbH & Co. KG, OptoMedical Technologies GmbH, Materialise GmbH, Dreve ProDiMed GmbH, microTEC Gesellschaft für Mikrotechnologie mbH, LPKF Laser & Electronics AG and the LZH.
The work is being funded within the call for proposals “Photonic Process Chains” within the framework of the programs “Photonic Research Germany” and “Material Technologies for Industry and Society (WING)” through the German Federal Ministry of Education and Research, and will be running for three years.