
Laser Technology Enhances Diver Safety in Sheet Piling Repairs
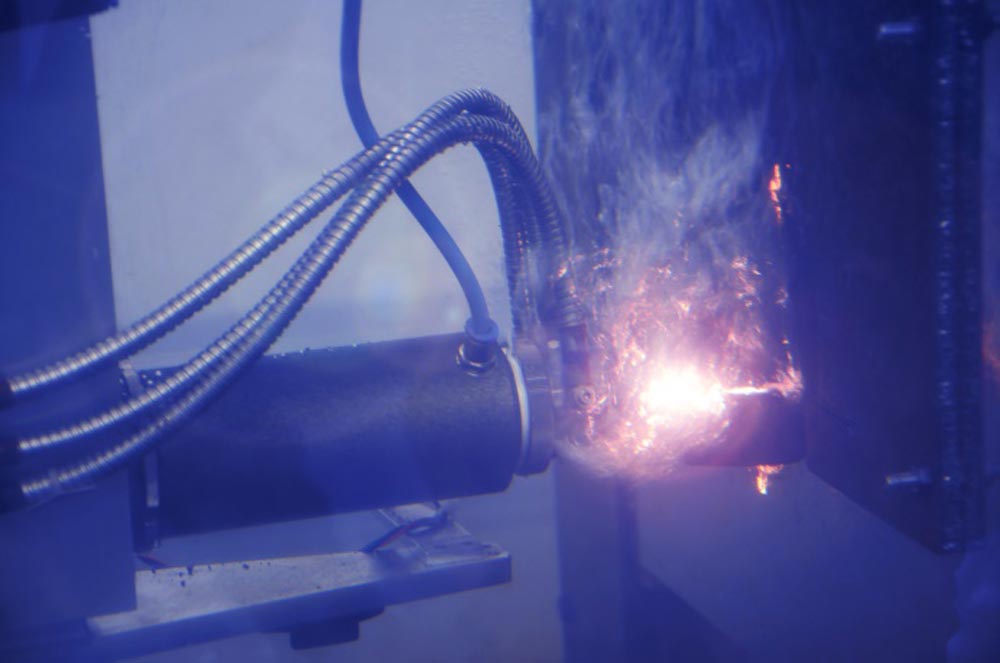
Metal sheets can be cut underwater by using a laser
Photo: LZH
Sheet piling protects fortified shore areas, or can be used to dry out these areas if repairs are necessary. If the sheet piling must be dismantled, divers must cut the walls into smaller pieces using a cutting torch. Normally, a diver can cut about 20 meters a day, which corresponds to a speed of about 0.07 meters per minute.
In the project LuWaPro, scientists at the LZH have now developed a process which uses a disc laser for torch cutting. The divers thus only carries out a supervisory role. The process can be used to separate the metal sheets, which are usually 10 mm thick for sheet piling, at speeds of up to 0.9 m/min.
Robust process despite unfavorable conditions
Poor visibility, currents or uneven surfaces make working underwater more difficult. The scientists of the Underwater Technology Group achieved a position tolerance of about two millimeters in their process, enabling the system to react robustly to possible impacts during underwater operation.
The process was tested with two scenarios: On the one hand, standalone metal sheets were cut underwater, on the other hand, the sheets were backfilled with concrete. In the second scenario, a leaking of the molten material through the cutting kerf is achieved by tilting the laser head at an angle of 20 degrees.
Through cuts?
A further major advantage in comparison to the hand-guided process is the possibility of monitoring the process. Sensors reliably determine whether a cut is completed or not. Otherwise the diver often cannot see this due to the poor visibility underwater.
Safe laser cutting under water
The laser safety necessary for this process can be guaranteed if the diver wears conventional safety goggles under the helmet.
The project “Laser cutting under water for high productivity – LuWaPro” was supported by the Federal Ministry for Economic Affairs and Energy.
Three figures and one video are available for this press release.