
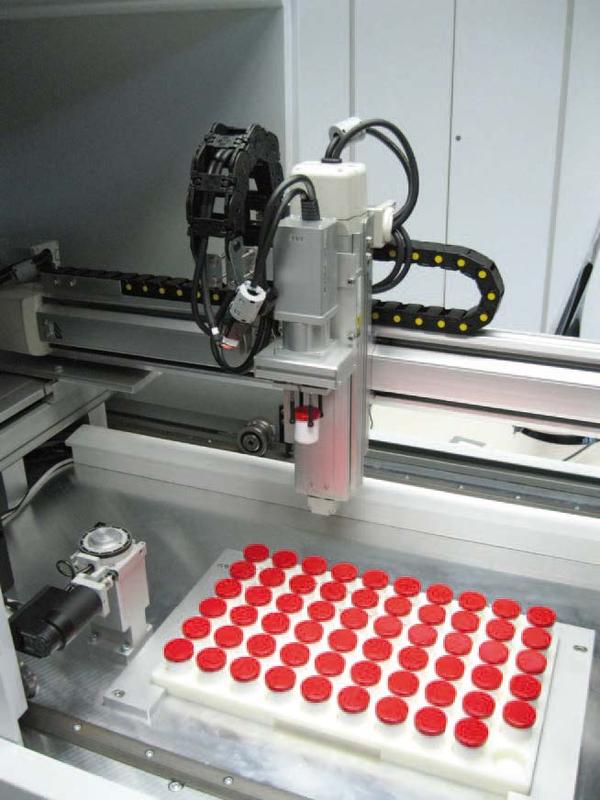
Fully automated laboratory system for industrial quality control
Fraunhofer IZFP
The CT Automat is used by Europe's leading seed producers to minimize seed rejects especially in case of sugar beet seeds to ensure at same time high-quality seeds, a “guaranteed germination rate”, and a steady.
This fully automated CT system was developed under the direction of Dr. Felix Porsch, group leader “3D X-ray CT” at Fraunhofer IZFP in Saarbrücken, Germany. “Compared to conventional radiography, computed tomography can provide much more detailed and especially quantitative information, as it provides the full volume information of each individual seed”, Dr. Porsch explains, whose team of scientists and engineers has adjusted this inspection method for use in seed production and then qualified it for industrial use in joint collaboration with industry partners as a nondestructive and fully automated inspection system that can be integrated into the quality control of virtually any manufacturing process of small parts.
“Our CT-Automat and its corresponding automatic image analysis software provide an easy way to considerably raise both, the number of random samplings and the reliability of the analysis results. As a consequence, the quality of the seeds has undergone a significant enhancement,” Dr. Porsch emphasized further.
But the scope of this “All-rounder” is not restricted to the evaluation of seed: A whole bunch of applications become accessible, e.g. the characterization of material samples (pore or particle size distribution) or bulk goods, or the integrity control of components.
This is true even for single parts within a large batch of small parts. In particular, samples of synthetic, organic or ceramic materials and light alloy are suited for tests with the X-ray machine. “Our automated CT system provides the opportunity to examine a large number of samples or components in a short time.
Thus, the system can be used in test laboratories for incoming goods inspection or even for production-related quality control. Depending on the object size a geometric resolution down to 20 micrometers is accessible; depending on the sample size and material, the recording time requires just a few minutes. Thus, up to 500 samples are testable per day”, Porsch continues.
Due to its compact size of a smaller cabinet, the CT system can be hosted in any laboratory area, with the complete X-ray technology, the sample changer and the control and computer technology inside the case. 24-hour continuous operation, auto-calibration and self-monitoring with reference samples are further advantages in favor of the integrated quality control in industrial series production: Time-consuming and costly procedures are a thing of the past.