
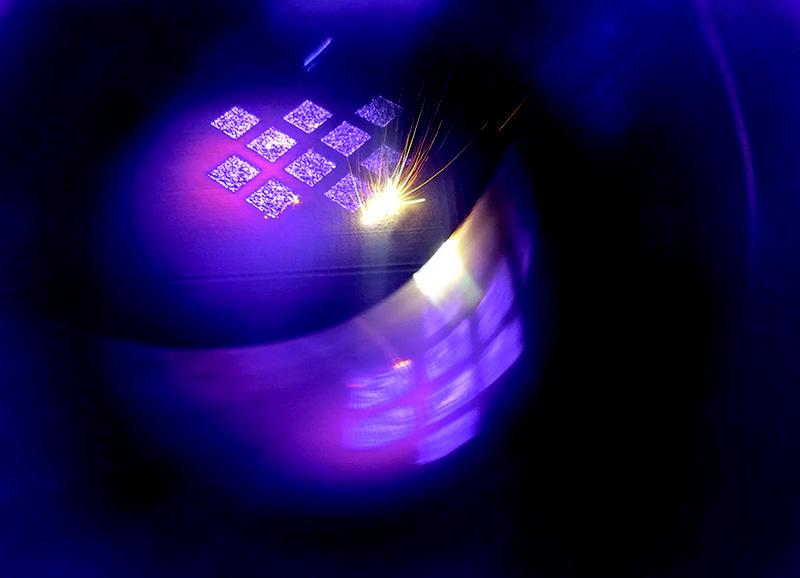
Exposure at local preheating using VCSEL.
© Fraunhofer ILT, Aachen, Germany
In just three years, formnext has established itself as the industry meeting place to get the latest on additive manufacturing (AM) processes. With 470 exhibitors and nearly 22,000 visitors, the fair in Frankfurt is also an international leader.
Located in Aachen, the Fraunhofer Institute for Laser Technology ILT has been involved in formnext right from the start. Its scientists have developed a lot of expertise in the field of additive manufacturing processes.
They work on a wide variety of AM topics, from increasing efficiency to developing system concepts and processes or even qualifying new materials. In Frankfurt, several Fraunhofer ILT experts will be present in Hall 3.0 at Booth E70.
Heating with kW power from above
As a highlight, the team of Fraunhofer ILT will be presenting a new process this year. This process – laser powder bed fusion (LPBF), also known as laser beam melting – can build parts with less thermally induced stress and less distortion than conventional process technology.
The internal stresses are caused by temperature gradients in the generated component: In the laser spot, temperatures above the melting point prevail, while the rest of the component cools rapidly. Depending on the geometry and material, this temperature gradient can even lead to cracks in the material. To avoid this, the component is usually heated from below via the substrate plate. However, that's not enough, especially with taller structures.
As part of the Digital Photonic Production DPP research campus, a funding initiative of the German Federal Ministry of Education and Research (BMBF), the experts from Fraunhofer ILT are working together with their partner Philips Photonics to develop solutions for this task. In the joint project DPP Nano, they have developed a set-up in which the component is heated from above.
For this purpose, an array of six vertical-cavity surface-emitting laser bars (VCSEL) with 400 W each is installed in the process chamber. With infrared radiation at 808 nm, this array can heat the device from the top to several hundred degrees Celsius during the building process. The bars can be controlled individually so that sequences of different patterns are possible. The process is monitored with an infrared camera.
In a concrete experiment, the Aachen engineers have constructed parts of Inconel® 718 and demonstrated significantly reduced distortion. The component was heated up to 500 °C.
The VCSEL heating reduces the thermal gradient, thus also the stresses, making it possible to produce taller parts. But even more interesting are the possibilities that arise for particularly difficult materials; soon, components made of titanium aluminides are to be produced. For this, the component will be heated to approx. 900 °C.
Such parts are commonly used, for example, in the hot gas section of turbochargers. In addition to turbomachinery, the process also opens up new prospects for other industrial sectors where thermally induced stresses in additive manufacturing processes have to be reduced.
More information will be available at the joint Fraunhofer Booth E70 in Hall 3.0 from November 13 to 16, 2018 at formnext in Frankfurt am Main. In addition, Andreas Vogelpoth will present the topic “VCSEL-Based Preheating for LPBF” at the TCT conference @ formnext on November 15, 2018 at 3.00 pm.
Further information about the Digital Photonic Production DPP research campus:
forschungscampus-dpp.de
Andreas Vogelpoth M.Sc.
Group Laser Powder Bed Fusion LPBF
Telephone +49 241 8906-365
andreas.vogelpoth@ilt.fraunhofer.de
Christian Tenbrock M.Sc. M.Sc.
Group Laser Powder Bed Fusion LPBF
Telephone +49 241 8906-8350
christian.tenbrock@ilt.fraunhofer.de
http://www.ilt.fraunhofer.de/en
http://www.forschungscampus-dpp.de