
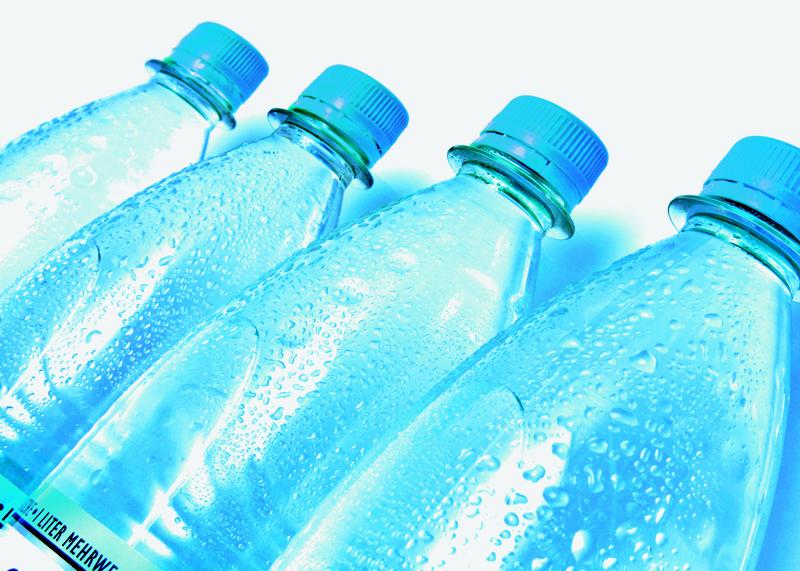
Scientists are researching how the upcycling of PET bottles can be economically viable and also protect the environment.
Foto: MEV-Verlag
Plastics are conquering the earth – unfortunately not always to the earth’s advantage, as indicated by the increasing reports on plastic waste. Two studies by the Fraunhofer Institute for Structural Durability and System Reliability LBF, on the other hand, demonstrate that upcycling of PET bottles and the recycling of flame-retardant plastics are worthwhile both for economic reasons and for protecting the environment.
Further details on these studies will be presented at the Compounding World Expo 2018 in Essen, from June 27 to June 28, at booth 707. Another main focus will be on new procedures in process technology, under the keyword Industry 4.0. A monitoring system that is based on intelligent sensor nodes, for example for a twin-screw extruder, ensures that networked work processes run reliably. With another patented procedure, the corrosiveness of plastic melts can be determined quickly, which also helps to prevent downtime in the future.
At the Compounding World Expo 2018, the Fraunhofer LBF will present information on an innovative procedure for the high-quality cycle utilization of polyethylene terephthalate (PET), which is being developed in the newly launched research project “UpcyclePET.”
PET waste from used beverage bottles is thus recycled as industrial plastic and thereby reduces the consumption of new plastic based on fossil resources. The project team consists of the company EASICOMP GmbH, the Fraunhofer Institute for Structural Durability and System Reliability LBF and the Öko-Institut. In order to develop an integrated manufacturing process for the production of glass fiber reinforced PET components, a pultrusion process is used, with which the PET plastic is reinforced with long glass fibers and thereby technically upgraded.
The special feature of this approach is to combine two process steps, which are separated in today's practice, and to tailor the properties of the recycled PET used by adding and modifying it.
Recycling Halogen-Free Flame Retardant Plastics
As a consequence of plastic production, disposal of these products at their end-of-life generates environmental challenges. Among the various disposal possibilities of plastics waste management, mechanical recycling is the favored option for ecological, economical and in particular energetic reasons. Polymeric waste materials are considered as valuable resources for manufacturing new products through recycling processes; preferably replacing virgin plastics provided similar properties can be achieved.
Due to the increased recycling quota there is a need to consider materials which are believed to be more demanding for mechanical recycling like flame-retardant applications of plastic. As part of a research project, the Fraunhofer LBF is investigating the mechanical recycling of various halogen-free flame retardants and polymer combinations.
The research is focused on the identification of aging behaviour and damage mechanisms after multiple extrusion cycles and accelerated thermo-oxidative aging, which can have a significant influence on the mechanical properties and fire behaviour. An understanding of the ongoing processes also allows tailor-made additivation with suitable additives. In this way, an improvement in the quality of recycled materials can be achieved. The results so far are promising. After multiple extrusion of PA6 and PA6 / GF (glass fiber) as well as PA66 / GF the flame retardancy of the formulations was maintained
Emissions from Plastic Products
The subject of emissions and odor from plastic products has been a major issue for many years, especially for plastics for indoor purposes, such as car interior. For many applications of plastic this question is considered having been solved. However, the industrial trend is going towards even lower thresholds. In addition, due to the increasing use of recycled material, the plastics industry is facing new challenges:
Recycled material exhibits higher emission potential. Furthermore the variation from batch to batch is quite broad, which always requires to adjust the process. Based on the many years of experience in this subject area, the Fraunhofer LBF is currently developing a process for on-line tracking of emissions, in which the emission behavior will be analyzed and documented during the compounding process. . Based on the measurement data, the recipe can be adjusted by means of different additives.
Optimizing Processes in Plastics Industry by Monitoring with Intelligent Sensors – Industrial Processes 4.0
Already today modern production systems can communicate with their surroundings and manage themselves. Industry 4.0 is on the rise and cyber-physical systems (CPS) are the essential components of this development. Intelligent sensors for monitoring and controlling production processes ensure that connected work processes can run reliably. Scientists at the Fraunhofer LBF have used these technologies as part of the “ImProcess4.0” project and developed an intelligent sensor node-based monitoring and optimization system for production lines using twin-screw extruders. This opens chances for predicted maintenance in production processes and thus reduces stand still times.
Determining the Corrosiveness of Plastic Melts Quickly
Abrasion and corrosion are serious problems in plastics processing, especially for some flame-retardant plastic compounds or the re-use of recycled material. Severe damage on screws, extruder housings, non-return valves or molds has been observed in this context.
In order to develop a high-performance compound, many different formulations have to be prepared through melt compounding and to be tested regarding the target properties and also the corrosiveness. Similarly, the problem arises when selecting the material for an aggregate to process a corrosive formulation. At Fraunhofer LBF an electrochemical screening method was devised primarily for development of polymer compounds and additives. The patented method makes it possible to assess rapidly the corrosiveness of a formulation even with low amount to be tested (approx. 1 kg).
It allows quick conclusions on the corrosiveness of a formulation. New raw materials or additives, that are initially available only in small quantities, can also be tested.
http://www.lbf.fraunhofer.de/de/veranstaltungen/messe-compounding-world-expo-201…