
Innovative Alternatives to Toxic Chemicals in Tire Manufacturing

Coating plant in the DITF
(c) DITF
The quality of composite systems made of cords of high-strength fibers such as polyester, aramid or polyamide and matrix materials of rubber is largely determined by the adhesion properties of the fibers to the matrix. In the established manufacturing process, adhesion promoters made of resorcinol-formaldehyde-latex (RFL) are used to improve the adhesion properties. Researchers at DITF are showing ways to replace the harmful formaldehyde with technically equivalent substances that are harmless to health.
In car tires, conveyor belts and V-belts, as well as in many applications in the manufacture of technical products, rubber materials are reinforced by cord. High-strength fibers made of polyester, polyamide or aramid are used. They provide the necessary strength and rigidity of the overall composite and counteract external forces. As a result, deformation, elongation and torsion of the material can be kept low.
However, these demands on the fiber composite material can only be met if there is sufficiently high adhesive strength between the fibers and the matrix (made of rubber or caoutchouc). Otherwise, delamination of the material composites, which are built up in alternating layers of fabric and rubber, is to be expected. Material failure would be the consequence.
Adhesion is increased by the use of adhesion promoters. Chemicals based on formaldehyde-resorcinol latex (RFL) have proven effective. They are applied to the fibers as so-called dips and ensure that their adhesion to the matrix of rubber is significantly improved. RFL is established as an adhesion promoter, but it has a significant drawback: since 2014, formaldehyde has been classified by the EU as demonstrably carcinogenic and mutagenic. The chemical industry is therefore urgently searching for alternatives that are harmless to health.
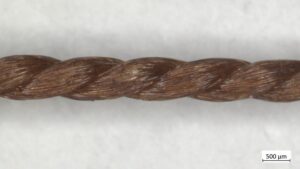
(c) DITF
DITF have tackled the problem and developed a new, formaldehyde-free coating system. It is based on the substance hydroxymethylfurfural (HMF), which can be extracted from wood. HMF is formed during the thermal decomposition of carbohydrates. It is found in many heat-treated foods such as milk, coffee or fruit juices and is not considered to pose any health problems according to current scientific knowledge.
The HMF dips developed at the DITF are also promising from a technical point of view: In the case of yarns made of polyamide 6.6, a simple impregnation is sufficient to achieve the desired adhesion improvement. Yarns made of polyester or aramid require an additional prior plasma treatment or a sol-gel finish to achieve the necessary adhesion improvement. Application of the HMF dip is possible under the same conditions and with the same technology used for RFL dips. At this point, therefore, no additional investment is required to replace the adhesion promoter in production.
The advantages already demonstrated are to be expanded. Replacing resorcinol in the dip formulation is the next research goal. This is because resorcinol also has a toxic effect on humans. In cooperation with industrial partners, the extent to which resorcinol can be replaced by lignin is currently being investigated. The special feature of the lignin used is that it is obtained from annual plants. Thus, in contrast to the frequently used wood lignin, it is chemically much more active and offers more potential for further processing into a technically advantageous adhesion promoter.
Both approaches to replacing chemicals in adhesion promoters with substances that are harmless to health carry the idea of sustainable management throughout: the new adhesion promoters made from HMF and lignin are based on natural raw materials. Solving the problem within a demanding, technical application while adhering to sustainability aspects reflects the commitments of research to societal requirements. For small and medium-sized industry, the research results provide the basis for innovations and thus a real advantage in international competition.
Wissenschaftliche Ansprechpartner:
Dr. Frank Gähr
German Institutes of Textile- and Fiber Research
Competence Center Textile Chemistry, Environment & Energy
Tel. +49 (0)711 / 9340-132
frank.gaehr@ditf.de