
Innovative Recycling Process for Precious Metals from Electrolysers
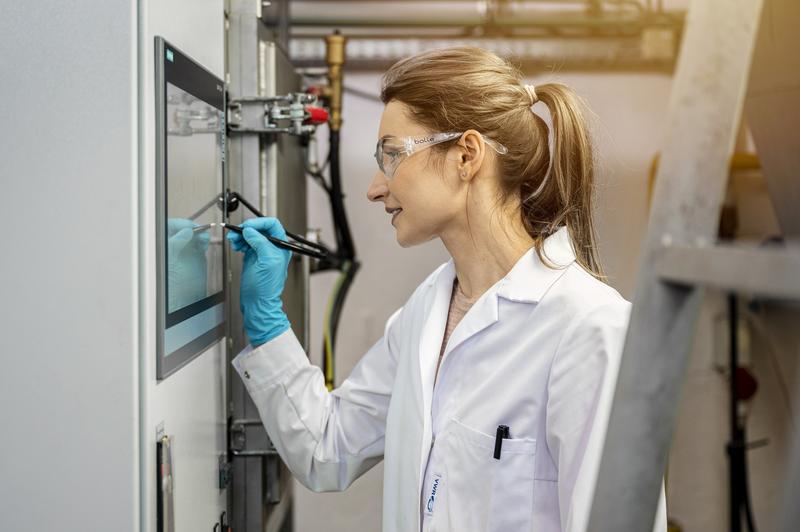
Dr. Lesia Sandig-Predzymirska in the lab.
(c) TU Bergakademie Freiberg / Crispin Mokry
Hydrogen from electrolysis with renewable energies is considered a key element of the energy transition. By means of catalysts, water is split into its components hydrogen and oxygen. The electrochemical reaction requires precious metals such as platinum, iridium or ruthenium as catalysts. How the recycling of these metals can be improved has been examined for three years by a European research project with the participation of TU Bergakademie Freiberg.
“Since the expensive precious metals in electrolysis cells cannot yet be completely replaced by other similarly efficient materials, the challenge is to recover them without loss. And this ideally with environmentally friendly processing,” explains project leader Prof. Alexandros Charitos fo TU Freiberg.
More environmentally friendly processing of end-of-life catalyst materials
The team focused on so-called hydrometallurgical recycling methods. This involves transferring the catalyst material into an aqueous solution and subsequently recovering it as a salt or metal in a solid form that is as pure as possible.
“The recovery of the various catalyst layers from precious metals, the heart of the proton exchange membrane electrolyzer (PEM electrolyzer), has so far required an energy-intensive and potentially environmentally harmful process step. “In the Recycalyse project, we are pursuing a recycling process in which the catalyst layers are separated from the fluorine-containing membrane,” explains Dr. Lesia Sandig-Predzymirska. The precious metals in the pre-concentrated catalyst layers can then be recycled with milder and more environmentally friendly leaching agents. “This produces starting materials that can be used directly for the production of new electrocatalysts to close the material cycle,” says the researcher.
New recycling method for precious metal ruthenium patented
A newly developed catalyst made of iridium and ruthenium proved to be the most efficient for the oxygen evolution reaction on the anode side of the cell. An antimony-doped tin oxide acted as the support material for the metals instead of carbon. “We have developed and patented a hydrometallurgical process using low-cost chemicals to efficiently recover ruthenium complexes that are valuable to industry,” says Dr. Lesia Sandig- Predzymirska. Ruthenium complexes are not only used in the chemical industry for the production of catalysts, but are also used in many other fields such as the electronics industry, medicine, biology, nanoscience and solar cell production.
Together with a newly developed separation process of the individual metal ions, the team achieved a metal recovery of more than 90% of the contained precious metals.
Electrolysis in focus of research
As storage of hydrogen from water electrolysis is an important building block for the energy transition, electrode materials are currently in the focus of research. In addition to the efficiency and availability of the materials, the “Recycalyse” project focuses particularly on their recyclability in the sense of the circular economy. It is led by the Danish Technological Institute and supported by nine other partners (TU Bergakademie Freiberg, Fraunhofer ICT, Sustainable Innovations, TWI, Blue World Technologies, University of Bern, Prüfrex, HyCentA Research GmbH and Accurec). Until the end of September 2023, “Recycalyse” will be supported with a total of 5.5 million euros from the European Union’s Horizon 2020 research and innovation program under grant agreement No. 861960.
Wissenschaftliche Ansprechpartner:
Prof. Dr.-Ing. Alexandros Charitos
Institute for Nonferrous Metallurgy and Purest Materials
+49 3731 39-2303
Alexandros.Charitos@inemet.tu-freiberg.de
Originalpublikation:
German Patent: Sandig-Predzymirska L, Barreiros TV, Thiere A, Weigelt A, Stelter M, Charitos A (2022) Verfahren zur Rückgewinnung von Ruthenium aus einem Ruthenium-haltigen Material; DE10 2022 111 440